
Figure 4.15A shows the elements involved in such a system. Part of such a system is concerned with delivering a constant pressure of fuel to the ignition system. For example, there is the engine management system aimed at controlling the amount of fuel injected into each cylinder and the time at which to fire the spark for ignition. The modern car involves many control systems. The change to the actual EGR is very small. The as mapped EGR value is simply multiplied by this derived factor. The EGR correction factor would range from less than 1% to 3%. This EGR correction was simply applied as a single factor for each fuel blend over all the modal points. As there was now a database of emissions values for each modal point with variation of EGR, a function was generated for EGR ratio to particulates and NOx.įrom these functions and the weighting of the modal points over the NEDC cycle an EGR correction factor was determined. With measured emissions for each modal point at a range of EGR amounts, further analysis was made to determine the EGR ratio correction required for each fuel.
#Extreme injector 3.7.1 series#
This second method was investigated further through a series of exhaust gas recirculation sweep tests conducted for each of the biodiesel fuel blends. Two obvious methods would be the use of injection strategy to recover the reduction in mixing efficiency or change the EGR mapped settings to achieve the same NOx levels. There are several methods to achieve this recalibration. The desired aim was to reduce the drive cycle NOx emission to be equivalent to the mineral diesel fuel NOx emission over an NEDC cycle. Abdullah, in Internal Combustion Engines: Improving Performance, Fuel Economy and Emissions: IMechE, London, 29–30 November 2011, 2011 5 DISCUSSION 5.1 Correction for the increase in NOx emissionsĪ further investigation was performed to determine the requirement of the engine management system to recover the increased NOx emissions for each of the biodiesel blends while maintaining some of the benefit of reduced particulates. By building this negative offset into the calibration, the OEM is simply recognising that deposits will inevitably form. This is deliberate, with the injector initially being held open for a shorter than nominal, extending the time before a dirty injector reaches its adaptive limit and triggers the engine malfunction indicator. It is also noticeable that the baseline injector adaption has an LTFT of below 0. As can be seen, the signal to the injector is holding it open for longer, compensating for the decreased flow rate through the injector due to deposit formation as a function of running time. In this example, a deliberately severe fuel has been used to reduce test duration, although the test drive cycle is itself mild, without any operation beyond 55 mph (90 km/h).
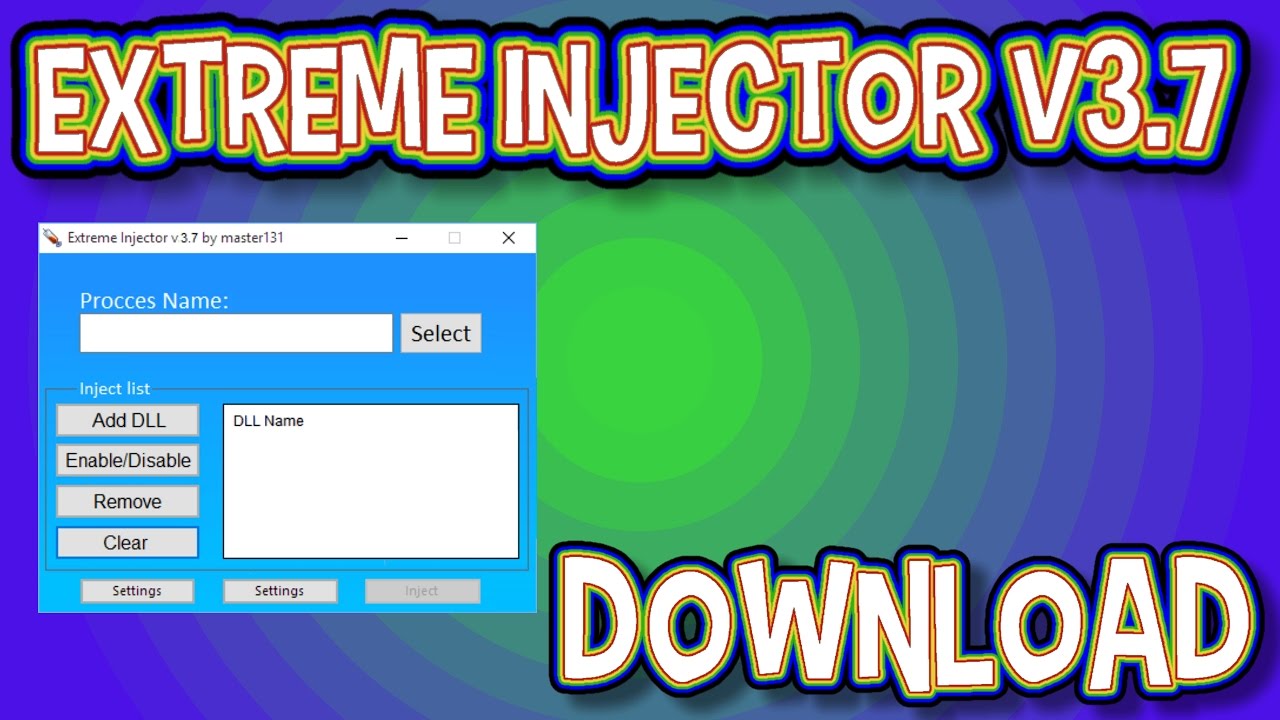
By interrogating the service diagnostic port, LTFT can be readily monitored as a function of running time, as shown in Figure 1. This compensation / adaption is known as Long Term Fuel Trim (LTFT), and provides a direct measure of flow loss and thus the amount of deposit in the injector nozzle. To compensate for this gradual shift, the EMS will increase the injector opening duration, returning the AFR to balance. As a fuel injector develops deposits, the rate of fuel flow through it will decrease, and the AFR will be become lean. This information is then fed back to the EMS which will adjust the fuel flow to maintain the correct AFR. Modern Engine Management Systems (EMS) use an oxygen sensor in the exhaust to monitor the air to fuel ratio (AFR).
